From rocks to solar cells: Silicon as the beating heart of solar panels
Every solar cell you see around, has a heart of rock! We, the process metallurgists working in the Department of Materials Science and Engineering, are responsible to provide the heart of the solar cells. Yes, the heart of the solar cell is a material called solar grade silicon (SoG – Si) which will start beating every second after mounting in a solar panel. This type of silicon (Si) must be free of impurities and requires especial methods for ingot production, like directional solidification or Czochralski (CZ). Figure 1 shows a Si ingot pulled from Si melt by CZ technique.
What is the solar silicon production value chain?
The story starts from reduction of quartz with carbon materials in a submerged arc furnace. The product is called metallurgical grade silicon (MG-Si) which can have purity up to 99%. This Silicon must be refined and should be free of Phosphorus (P) and Boron (B). The following steps can be named as the major steps in the value chain of solar cell production:
- The quartz rocks must be converted to Silicon.
- The silicon must be refined to SoG – Si (99.9999 % pure).
- Si ingot production from the refined Si (Figure 1).
- The refined Si requires to be sliced.
- The silicon wafers require to receive the Phosphorus and Boron emitter layer.
- The solar cells are now born and can be installed on a panel to make solar cells.
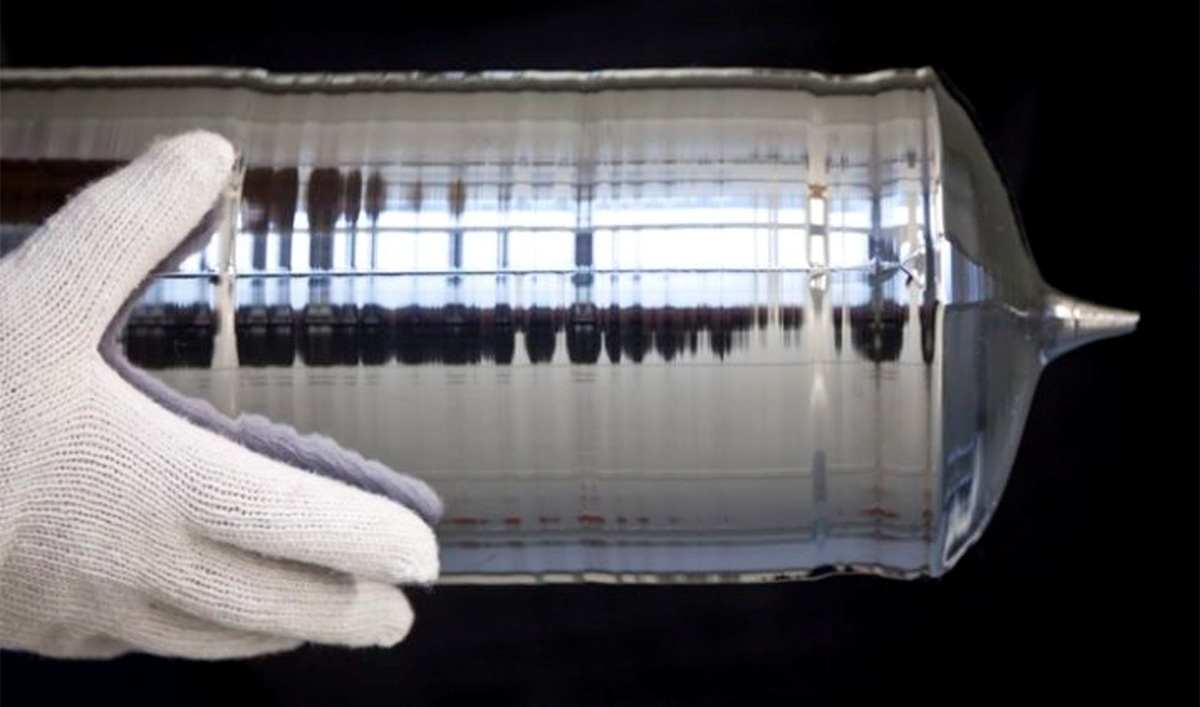
What is the challenge in SoG-Si production?
Silicon production has a long history in Norway, however, refining of Silicon is something different. I would say, Si refining is the most difficult step and the challenge is the removal of Phosphorus and Boron elements. These two elements like to stay in Si and dedicated removal techniques are required for removal of these elements.
What are the typical refining techniques for purification of Silicon?
The oldest technique is known as Siemens, which produces electronic silicon with the purity of 10 – 12N. N purity refers to the number of 9’s (10-12N means 99.99999999-99.9999999999% silicon). However, for production of solar cells, we do not need this quality and 6N is enough. Fluidized Bed Reactor (FBR) is an American technology able to produce 8N – 12 N purity of silicon.
In both the Siemens® and FBR® technologies, high amount of energy is required for refining of Si. However, Metallurgical methods for production of SoG-Si were introduced in early 2000 and currently at least three of them are in industrial level or tested in large scale [1–3]. These methods are more energy efficient and environmentally friendly for SoG-Si production. A summary for the clean Si production could be found in the Figure 2 where the timeline for various methods leading to production of SoG-Si and Electronic Grade Silicon (EG-Si – purity requirements 10 – 12 N) are shown. Elkem solar® started the first metallurgical plant for refining the Metallurgical grade silicon (MG-Si – purity requirements 2 N) to SoG-Si in 2007 by a process containing slag refining and leaching processes. Slag refining is a process in which a Si melt gets purified by a slag phase. Slag is usually a mixture of CaO – SiO2 oxides. During this process the impurities migrate from Si melt to the slag phase. The slag is then a by-product of the slag refining process and must be disposed. The production of 1 kg SoG – Si usually requires leads to 1 kg disposal of slag. Leaching process is a process for dissolving of materials in acids. For the case of Si, the metallic impurities can be dissolved in hydrochloric acid while Si does not dissolve in HCl, and then can be purified. The acid leftovers remained after the leaching process require neutralization before disposal.
Silicor Materials, a manufacturer of high-quality solar silicon, started pilot production of SoG-Si in 2009 by solvent refining of Si by Aluminium (Al) addition-solidification, and a subsequent leaching process. The last metallurgical method added to the market is the Ferroglobe® (silcio ferro solar) technology which produces the solar silicon by slag and vacuum refining. Vacuum refining is a process in which Si melt is being treated in a closed chamber, while the chamber atmosphere is being continuously sucked out by a vacuum pump. During this process the pressure in the chamber can even reduce down to 1 Pascal (in reference the atmosphere pressure is 101325 Pa). During the vacuum refining process, all the elements that have a higher vapor pressure than Si melt, will evaporate from Si. Phosphorus can be removed 100 % in this process. There is no by-product in vacuum refining, making this process environmentally friendly.
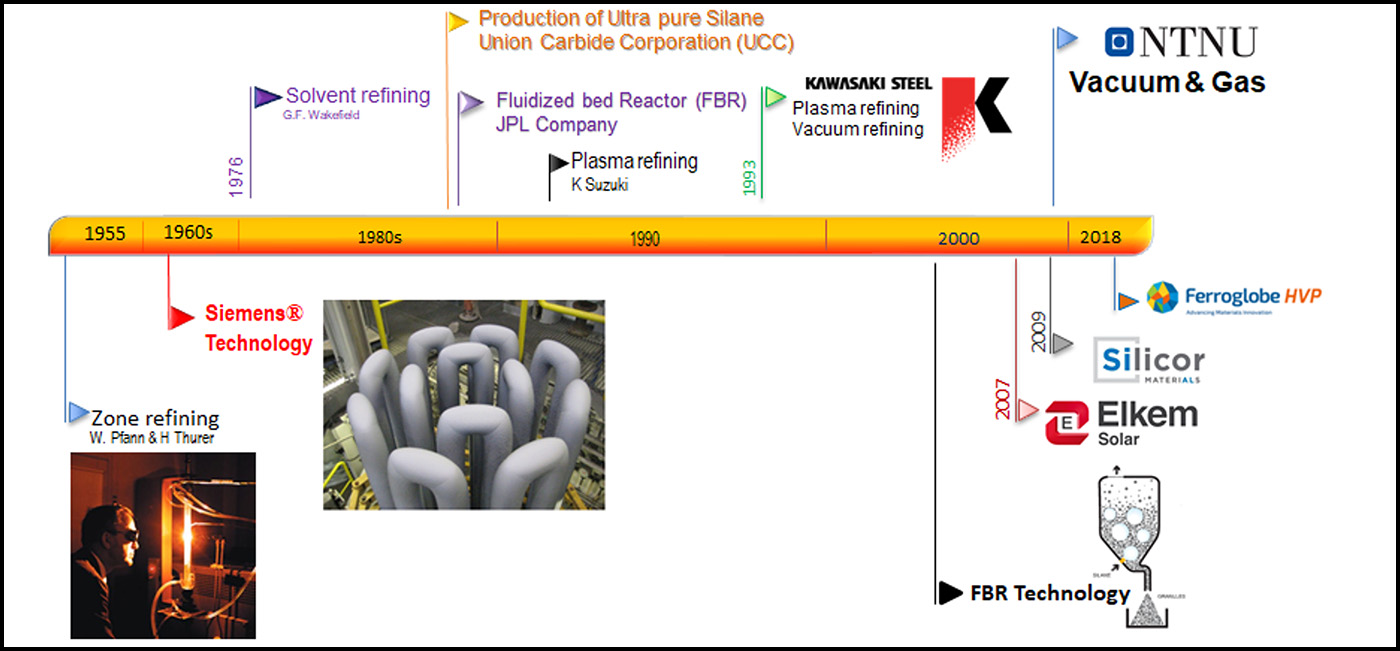
What approach does NTNU have for SoG-Si production?
Currently there are some researchers collaborating with Elkem for improving the slag – leaching technology. In addition, from 2008, a series of researches has started in NTNU with collaboration of SINTEF and Elkem, focusing on vacuum and gas refining techniques [4–8]. Preliminary results indicate these methods are energy efficient, and produce much less byproducts compared to other metallurgical refining techniques. Figure 3 shows the schematic of the vacuum-gas refining method under research in NTNU. During the course of the vacuum refining, Phosphorus will evaporate and then Si can be refined in gas refining step. Important advantage of this process is to have all the refining steps at molten state, without needing to solidification and melting leading to saving energy consumption.
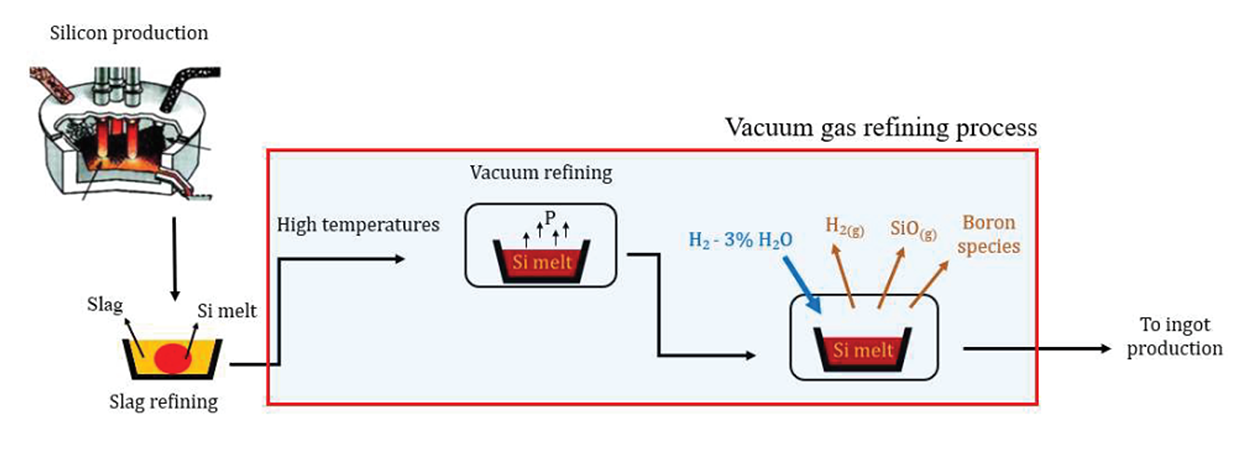
What are the benefits of the new refining methods?
When comparing the NTNUs’ approach (vacuum and gas refining) with other techniques, we will see it is independent of thermodynamics equilibrium. In other words, in all the other metallurgical methods, a thermodynamic equilibrium establishes between the Si and the refining phase (slag or liquid metal) and then further removal is not possible. However, in the case of vacuum and gas refining, the removal process never stops and the refining process can be continued until reaching the required limit for the solar cells. Over the past decade, lots of research are carried out in vacuuma and gas refining processes in the lab scale experiments. Thanks to the new furnace commissioned in 2018, it is time to scale up the process up to 20 kg. Figure 4 shows the new pilot furnace for large scale experiments.
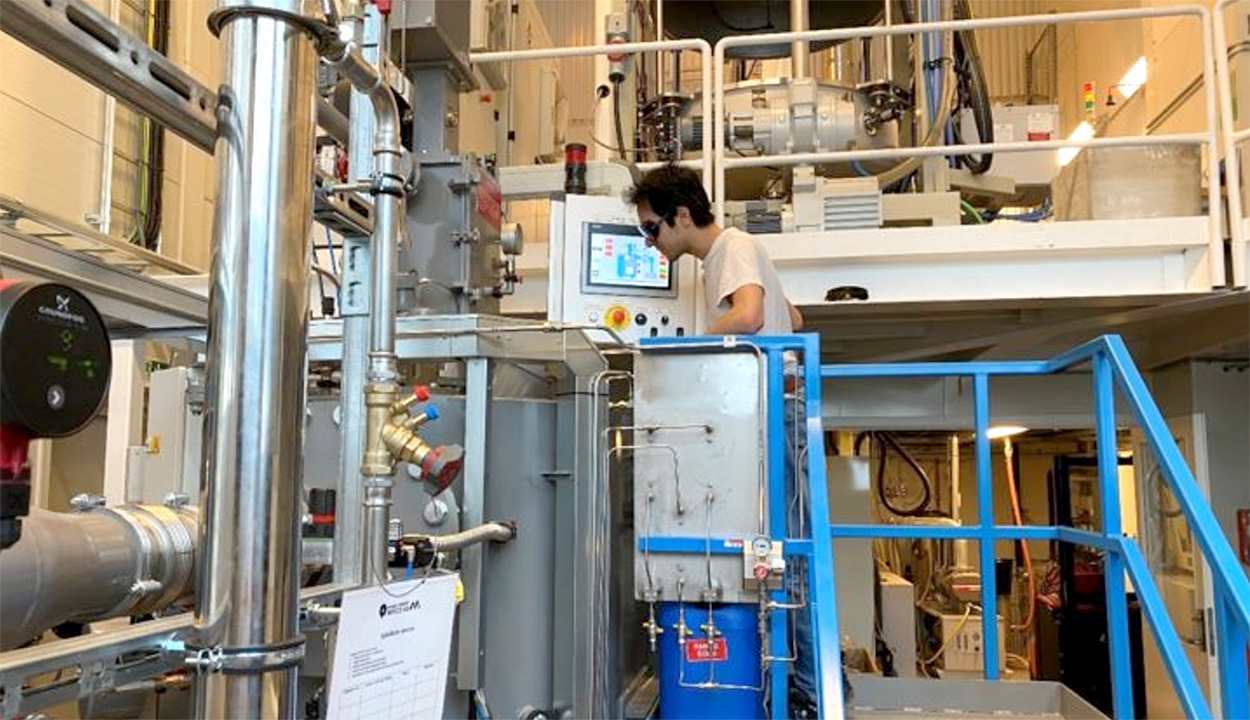
For Further reading
- Silicor Materials
- A. Murgau, J. Safarian, solar silicon production through metallurgical route and REC solar advancements, in: Silicon Chem. Sol. Ind., Avolvær, 2018: pp. 18–192.
- Forniés, Ceccaroli, Méndez, Souto, Pérez Vázquez, Vlasenko, Dieguez, Mass Production Test of Solar Cells and Modules Made of 100% UMG Silicon. 20.76% Record Efficiency, Energies. 12 (2019) 1495. doi:10.3390/en12081495.
- J. Safarian, K. Tang, K. Hildal, Vacuum treatment of ferrosilicon, in: 2015 Sustain. Ind. Process. Summit, 2015: pp. 261–268.
- J. Safarian, T.A. Engh, Vacuum Evaporation of Pure Metals, Metall. Mater. Trans. A. 44 (2013) 747–753. doi:10.1007/s11661-012-1464-2.
- J. Safarian, B.S. Xakalashe, M. Tangstad, Vacuum removal of the impurities from different silicon melts, in: 26th Eur. Photovolt. Sol. Energy Conf. Exhib. Vac., 2011: pp. 1810–1813. doi:10.4229/26thEUPVSEC2011-2BV.4.3.
- A. Hoseinpur, S. Andersson, K. Tang, J. Safarian, Selective Vacuum Evaporation by the Control of the Chemistry of Gas Phase in Vacuum Refining of Si, Langmuir. 37 (2021) 7473–7485. doi:10.1021/acs.langmuir.1c00876.
- A. Hoseinpur, J. Safarian, Vacuum refining of silicon at ultra-high temperatures, Vacuum. 184 (2021) 109924. doi:10.1016/j.vacuum.2020.109924.
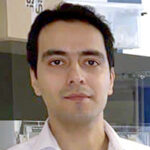
Arman H. Kermani
Arman H. Kermani is a researcher at the Department of Materials Science and Engineering. He is a member of the Resources, Energy & Environment research group.
Tags In
Search
Søk
Categories
- Arctic Research
- Arkitektur
- Bærekraft
- Bioingeniørfag
- Biologi
- Biology
- Biomedical Laboratory Science
- Biotechnology
- Bioteknologi
- Chemical Engineering
- Chemistry
- Climate
- Computer Science
- Datateknologi
- Digital
- Elektronikk
- Energi
- Energi
- Energy
- Engineering
- Engineering
- Environment
- Food Science
- Forskning
- Fysikk
- Fysikk
- Havbruk
- Informasjonsteknologi
- Informasjonsteknologi
- Ingeniørvitenskap
- Kjemi
- Kjemisk prosessteknologi
- Kjemisk prosessteknologi
- Kreftbehandling
- Kybernetikk
- Marine Technology
- Materialer
- Materials Science
- Materialteknologi
- Matvitenskap
- Meninger
- Miljø
- Min ph.d.
- My PhD
- My PhD
- My postdoc
- Nanotechnology
- Nanoteknologi
- Ocean
- Oil and gas
- Physics
- Research
- Simulering og visualisering
- Spør en forsker
- Studentliv
- Sustainability
- Ukategorisert
- Universitetsliv
- University Life
Kategorier
- Arctic Research
- Arkitektur
- Bærekraft
- Bioingeniørfag
- Biologi
- Biology
- Biomedical Laboratory Science
- Biotechnology
- Bioteknologi
- Chemical Engineering
- Chemistry
- Climate
- Computer Science
- Datateknologi
- Digital
- Elektronikk
- Energi
- Energi
- Energy
- Engineering
- Engineering
- Environment
- Food Science
- Forskning
- Fysikk
- Fysikk
- Havbruk
- Informasjonsteknologi
- Informasjonsteknologi
- Ingeniørvitenskap
- Kjemi
- Kjemisk prosessteknologi
- Kjemisk prosessteknologi
- Kreftbehandling
- Kybernetikk
- Marine Technology
- Materialer
- Materials Science
- Materialteknologi
- Matvitenskap
- Meninger
- Miljø
- Min ph.d.
- My PhD
- My PhD
- My postdoc
- Nanotechnology
- Nanoteknologi
- Ocean
- Oil and gas
- Physics
- Research
- Simulering og visualisering
- Spør en forsker
- Studentliv
- Sustainability
- Ukategorisert
- Universitetsliv
- University Life