How much energy is required to prevent ice on UAVs?
In-flight icing of UAVs is a severe hazard that prevents drone operations in bad weather conditions. In order to overcome this limitation, UAVs can be equipped with ice protection systems that mitigate the negative effects of icing. One solution is to heat the exposed surfaces of the aircraft electrically with carbon fiber materials. The big question is how much (or rather how little) energy is required to prevent ice from building on the aircraft.
In this paper, we investigated several designs of such electrothermal ice protection systems in collaboration with UBIQ Aerospace. Our goal was to find out how different designs and operation modes affect the required energy for ice protection. We tested two systems in an icing wind tunnel at the Technical Research Centre of Finland (VTT) in Helsinki. An icing tunnel is a facility where icing conditions can be simulated under laboratory conditions.
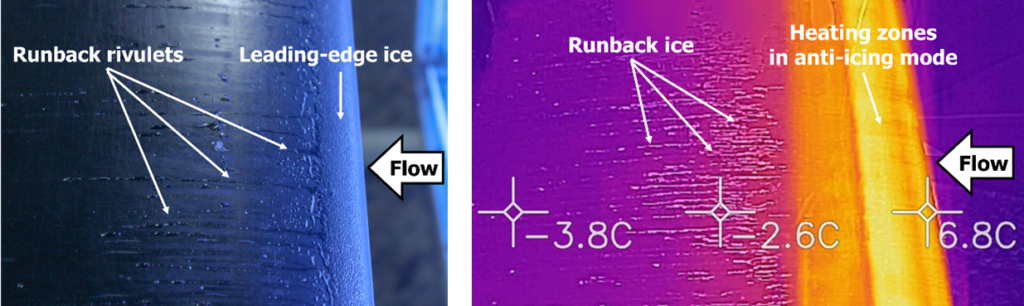
The experiments showed that de-icing with parting strip gives the most energy-efficient ice protection. De-icing means that the ice protection system is not operating continuously (which is called anti-icing). Instead, the system allows for uncritical amounts of ice to build-up on the airframe, which is then periodically removed by heating the surfaces. In practice, we allow ice to build up over a few minutes (typically 2-4min) and then heat for about 10-30s. In addition, we use a parting strip. A parting strip is essentially a continuously heated wire that creates a “gap” in the ice that builds on the leading edge of the wings. Instead of having a continuous ice accumulation, the parting strip separates them into an upper and lower part. The advantage of this gap is that it gives the aerodynamic forces a larger area and longer leverage for acting on the ice. This means that the incoming airflow now “helps” to shed ice by exerting an additional shedding force on the ice accumulations. In practice, parting strip ice protection systems de-icing a wing substantially faster compared to de-icing without parting strip.
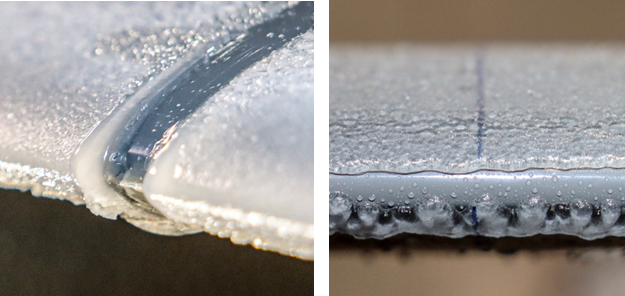
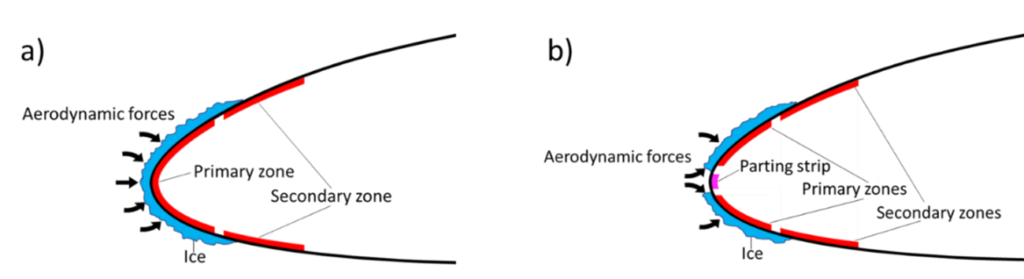
In summary, these experiments will help us improve the design of ice protection systems. The results will be used to increase the energy-efficiency of ice protection systems. As a consequence, UAVs can safely fly for longer durations in icing conditions. This is an important step for unlocking many new applications of unmanned aircraft such as package deliveries, search & rescue operations, or even passenger transports in urban air mobility.
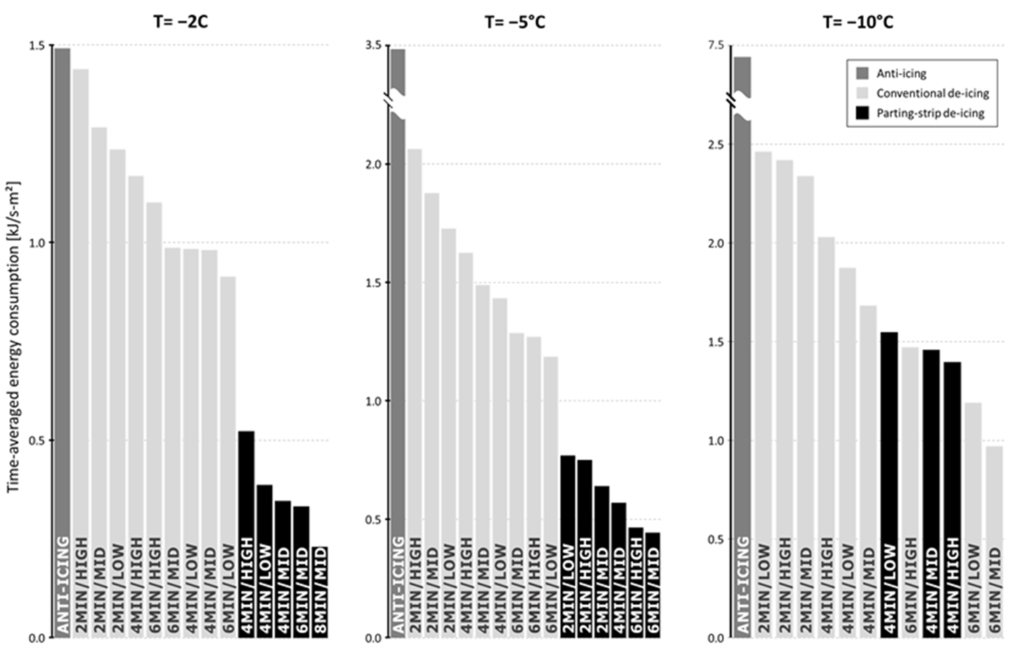
Reference: Hann, R., Enache, A., Nielsen, M.C., Stovner, B.N., van Beeck, J., Johansen, T.A., Borup, K.T. (2021). Experimental Heat Loads for Electrothermal Anti-Icing and De-Icing on UAVs. Aerospace, 8(3), 83. DOI: 10.3390/aerospace8030083