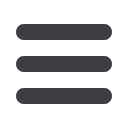
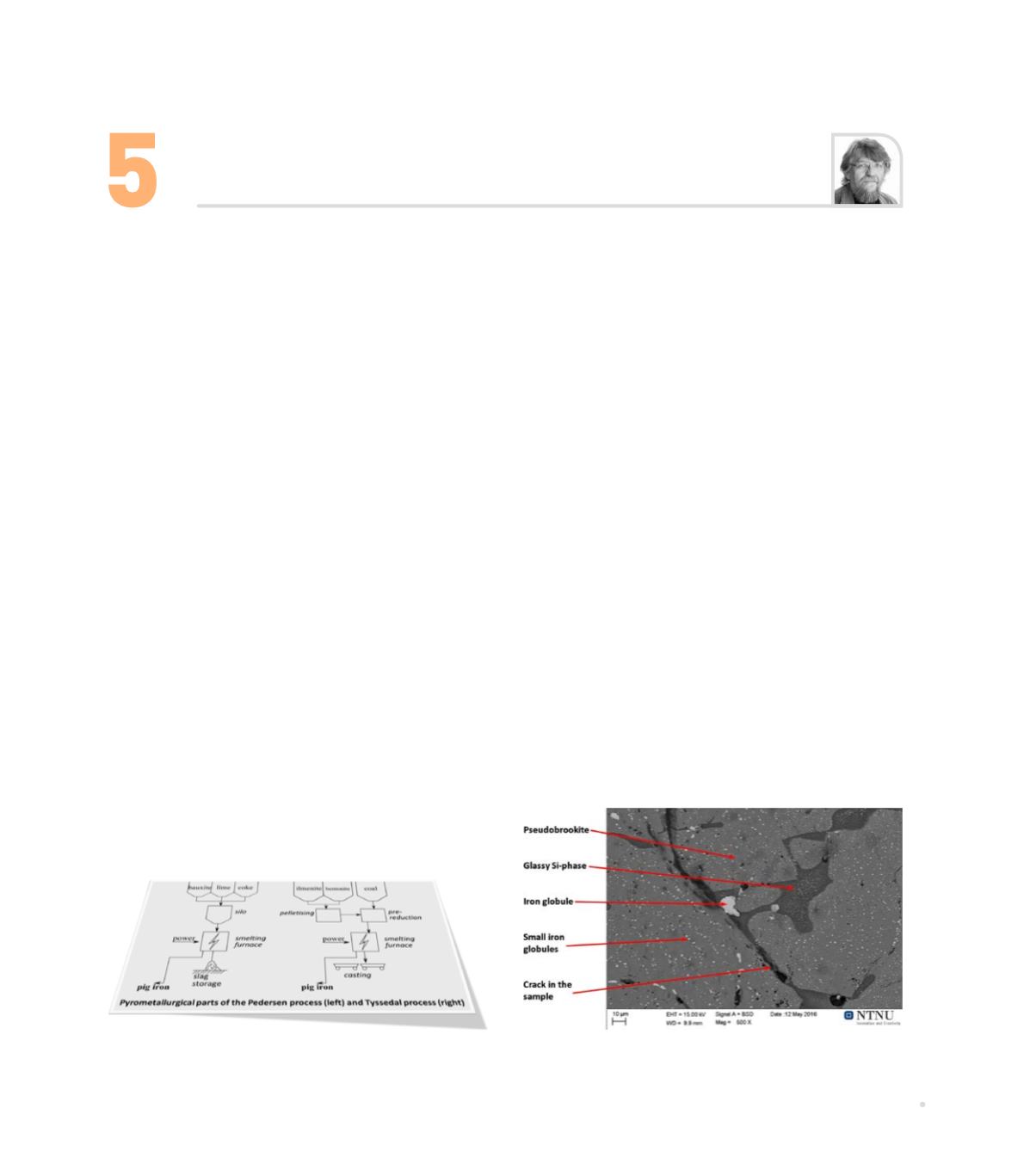
Material Flow Analysis (MFA):
Professor Daniel Müller
(Industrial Ecology) is essential in the RD5 activities in
this field. This activity also involve cooperation with the
EU-projects:
i.
MinFuture:
Global Material Flows and Demand-
Supply Forecasting for Mineral Strategies,
ii.
MICA:
Minerals Intelligence Capacity Analysis &
iii.
MINEA:
Mining the European Anthroposphere
What if the iron in bauxites is removed before it be-
comes “waste”?
One obvious way to deal with the Bayer
Process Bauxite Residue (BPBR or Red Mud) is to re-
move the iron from the Bauxite at an early stage of the
Alumina-production. This problem has been addressed
by master student Hanne Sellæg in “Pedersen Process
for Alumina Production” under the supervision of Jafar
Safarian.
The Pedersen process is in principle capable of produc-
ing Alumina from Bauxites and Laterites in general via
an intermediate slag product, while the iron in raw ma-
terials is converted into a commercially viable product
(pig iron). This slag is treated further in a Na
2
CO
3
solu-
tion without generating Red Mud and CO
2
from calcining
is utilised for precipitation of aluminium hydroxide. This
process strongly resembles the Tyssedal Process where
a Titania (TiO
2
) slag is produced along with iron from
Ilmenite (FeTiO
3
). The knowledge generated will be put
to use in adjacent projects and initiatives.
Solidification of Titania Slag:
Ilmenite is a titanium-rich
ore, and accounts for almost all the world’s consumption
of titanium bearing minerals. One of the main uses of ti-
tanium is as powdered TiO
2
, used extensively as whiten-
ing pigment. The first step in the process of making TiO
2
pigment is reducing the ilmenite to a titanium-rich slag.
The slag needs to be purified and processed to make
the pigment product. The MSc thesis by Rune Stana,
“Solidification of Titanium Slags and Influence on Post
Processing”, focuses on the stage after reducing the il-
menite to a titanium-rich slag, and before the further
purification of the slag. To get a better understanding
of the properties of the solid slag after reduction in the
blast furnace, both industrially collected and experi-
mentally prepared samples have been analysed. It is be-
lieved that the cooling rate and access to oxygen of the
slag during solidification will influence the micro-struc-
ture of the solidified slag. This gives rise to differences
in both grain size and shape, as well as the phases pres-
ent. This work continues in RD2.
Green Industry Clusters/Industrial Parks:
Work on a
“Cluster Model” is initiated. The main scientist in this ac-
tivity is Magne Lysberg of Sintef Materials & Chemistry.
Materials and Society (RD5)
by Professor Leiv Kolbeinsen
19
Highlights of 2016 from the Research Domains